
ChemArt Automated Stringer
Assembly Line Addition.
As part of the URI Engineering program, a Capstone design project paired with a company was the final test for engineers before graduation. I was the lead of Team 7, with the responsibility for three other colleagues. As the team lead, I controlled all of the decisions made within the team whether that be design, budget, or construction. I was also the spokesperson for the team in meetings, calls, and presentations. My team was paired with ChemArt, which an excerpt from my interim design paper below will explain.
ChemArt is an ornament manufacturing company with their headquarters located in Lincoln, RI. They produce ornaments for many sectors, some of which include non-profits, national parks, retail, government, and military, with their highest volume ornament being produced for the White House Historical Association. ChemArt currently uses a 17-step manufacturing process to produce each ornament. Over the years they have had problems with their production costs. While labor rates and material costs have increased, ChemArt’s clients aren’t willing to pay more for the same product. The company has also had an increase in the order volume that needs to be accounted for. To combat this, they must find steps in their process where they are able to cut costs without decreasing production.
Our team was tasked with developing a process to improve the current ornament ribbon tying process at ChemArt. Currently, the company uses a group of six to eight workers to string and tie the ornaments completely by hand right before they are packaged for sale. This process however can prove to be very slow and by effect rather costly. Currently the best employee is able to output 105 ornaments per hour with a labor rate of $11.50 per hour. This works out to a unit price of $0.11 per unit for this step in the production process. The company however is fine with this unit price if it means that the workers can get paid more without increasing the unit price for this step of their production process. ChemArt plans on raising the workers’ wages to $16.50 per hour. Therefore, they need to raise production to a minimum of 150 units per hour or more, so the unit prices remain at $0.11. To do this the team was assigned with making a mechanism, whether it be fully autonomous, semi-autonomous, or completely manual that will increase the production rate to 150 units per hour without raising the unit price. It is assumed a machine will work at 80% efficiency. So, to achieve the output of 150 units per hour a machine would have to operate at a minimum of 187.5 units per hour.
We had two working designs for the string insertion method. Below is a collection of designs and drawings created by me to showcase our idea in its rough stages. I've also included some images taken along the way. Some models were simplified in the rendering for time efficiency but full details can be found in the drawings. The robotic arm we used was supplied to us by ChemArt as they had a spare. We used pneumatic actuators and stepper motors for our design as ChemArt has in-house air.
Main rendering of working design.
Basic gif of operation order.
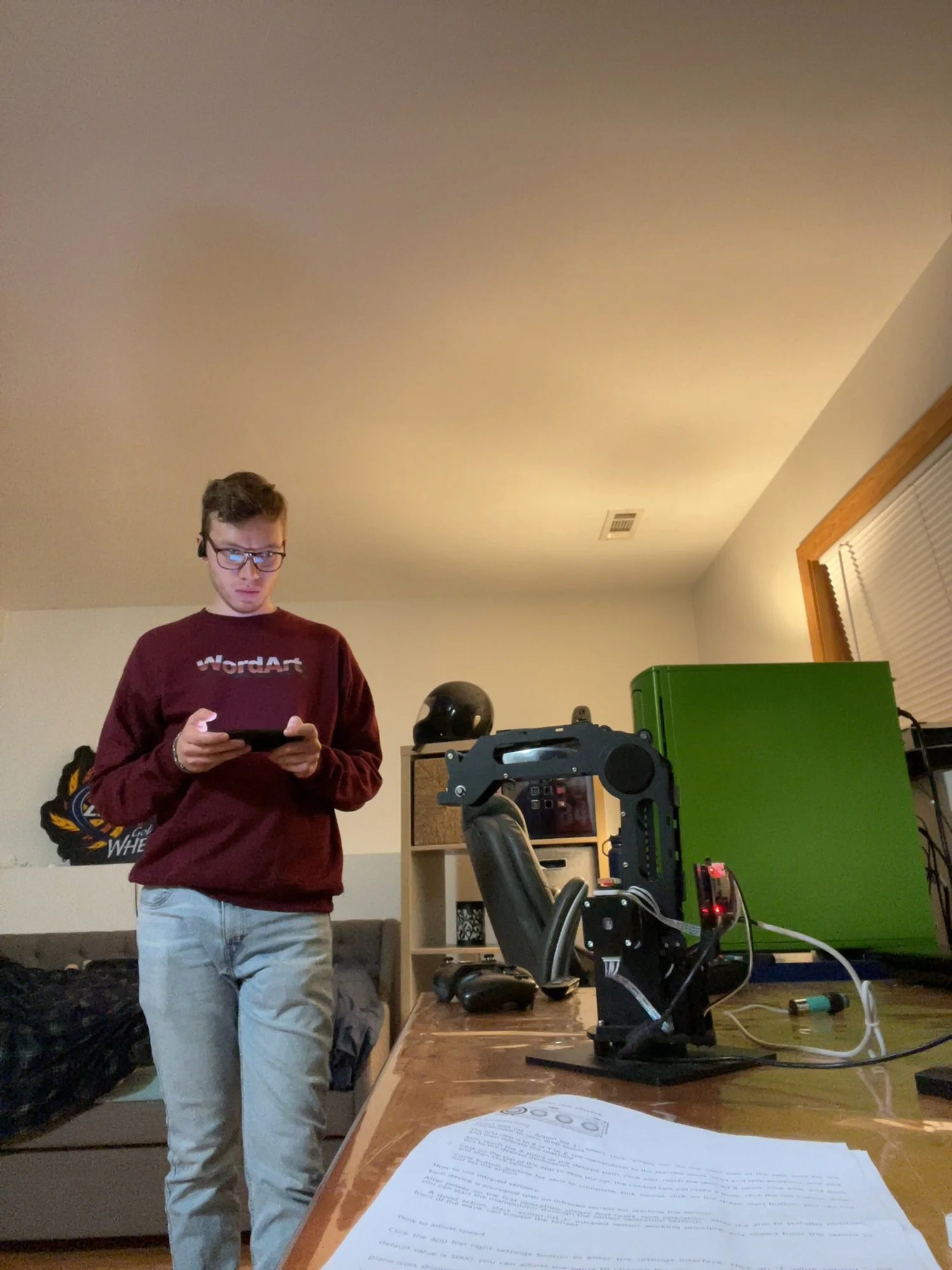

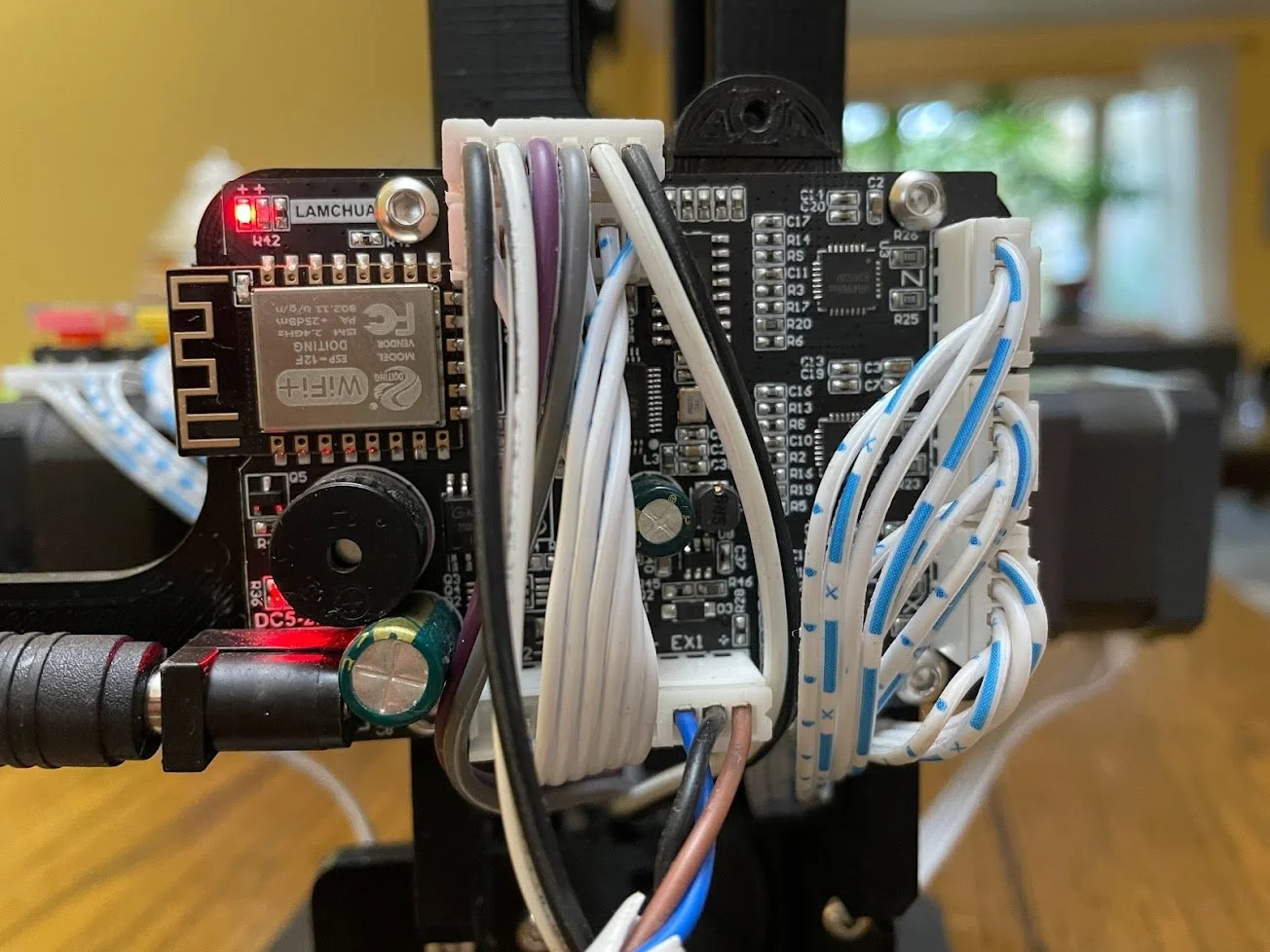
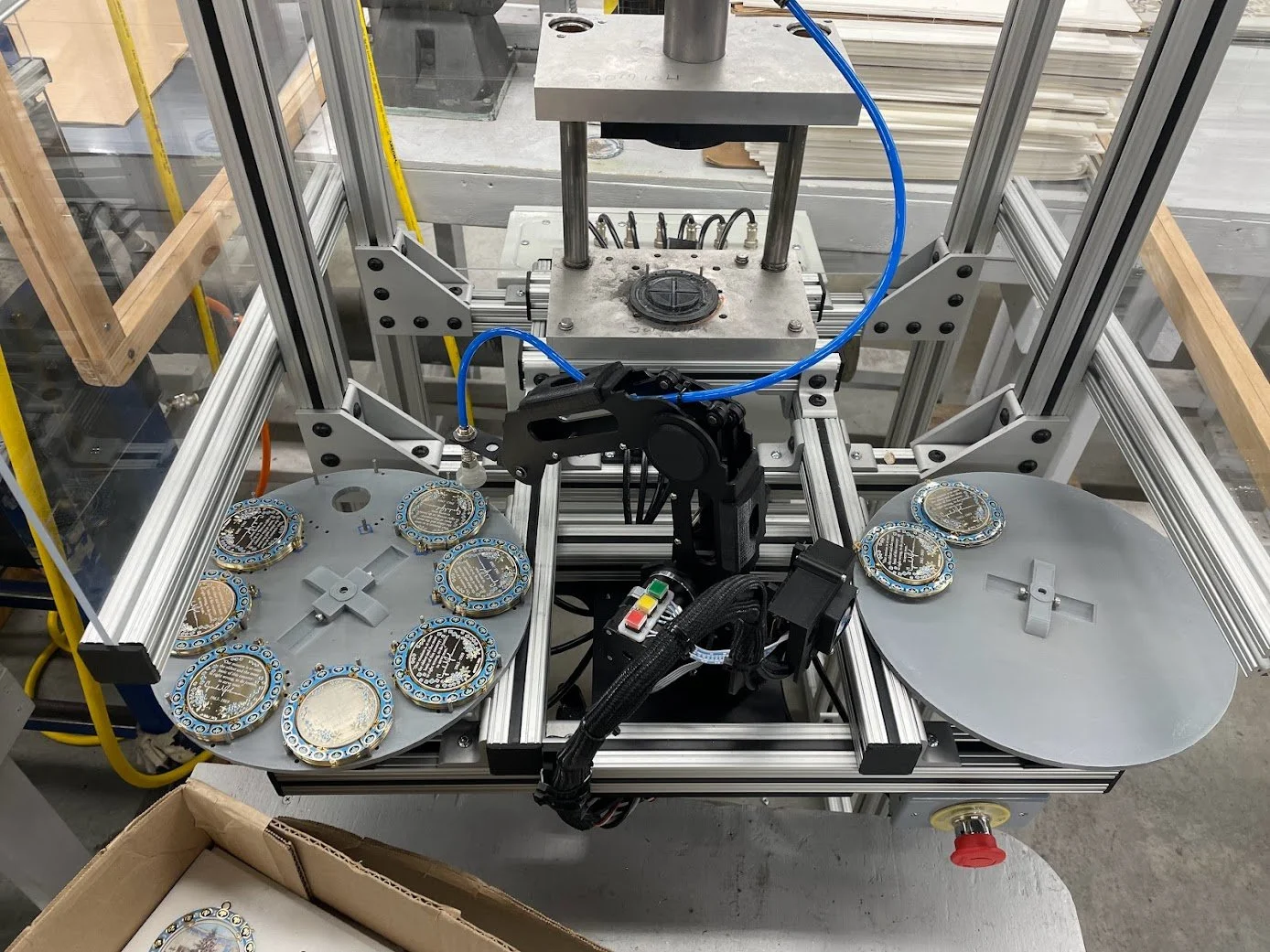


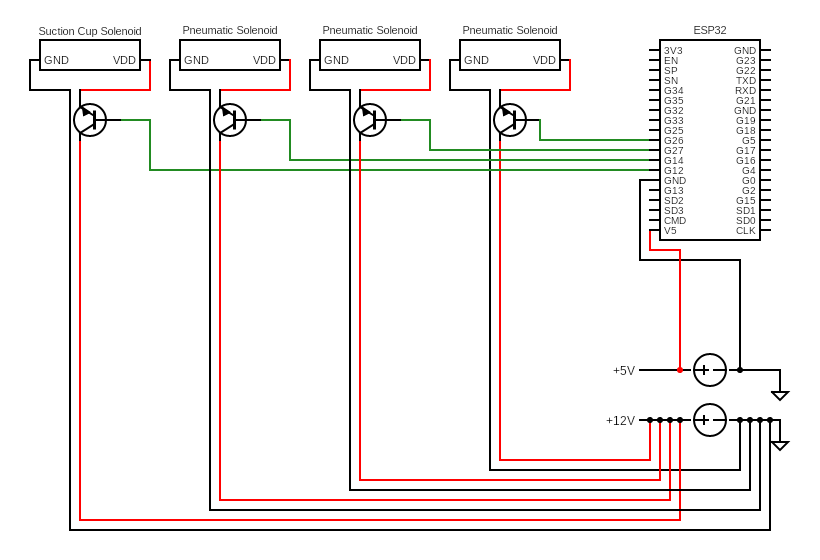
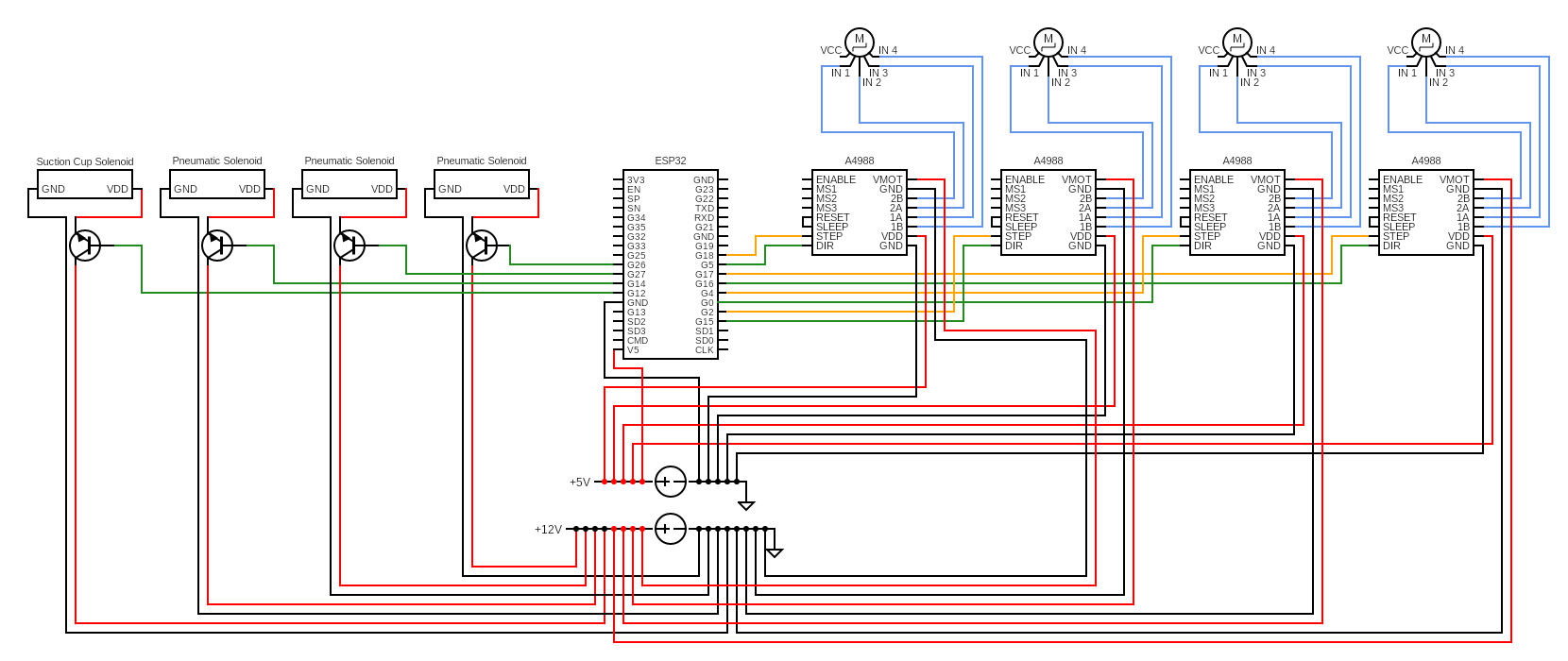
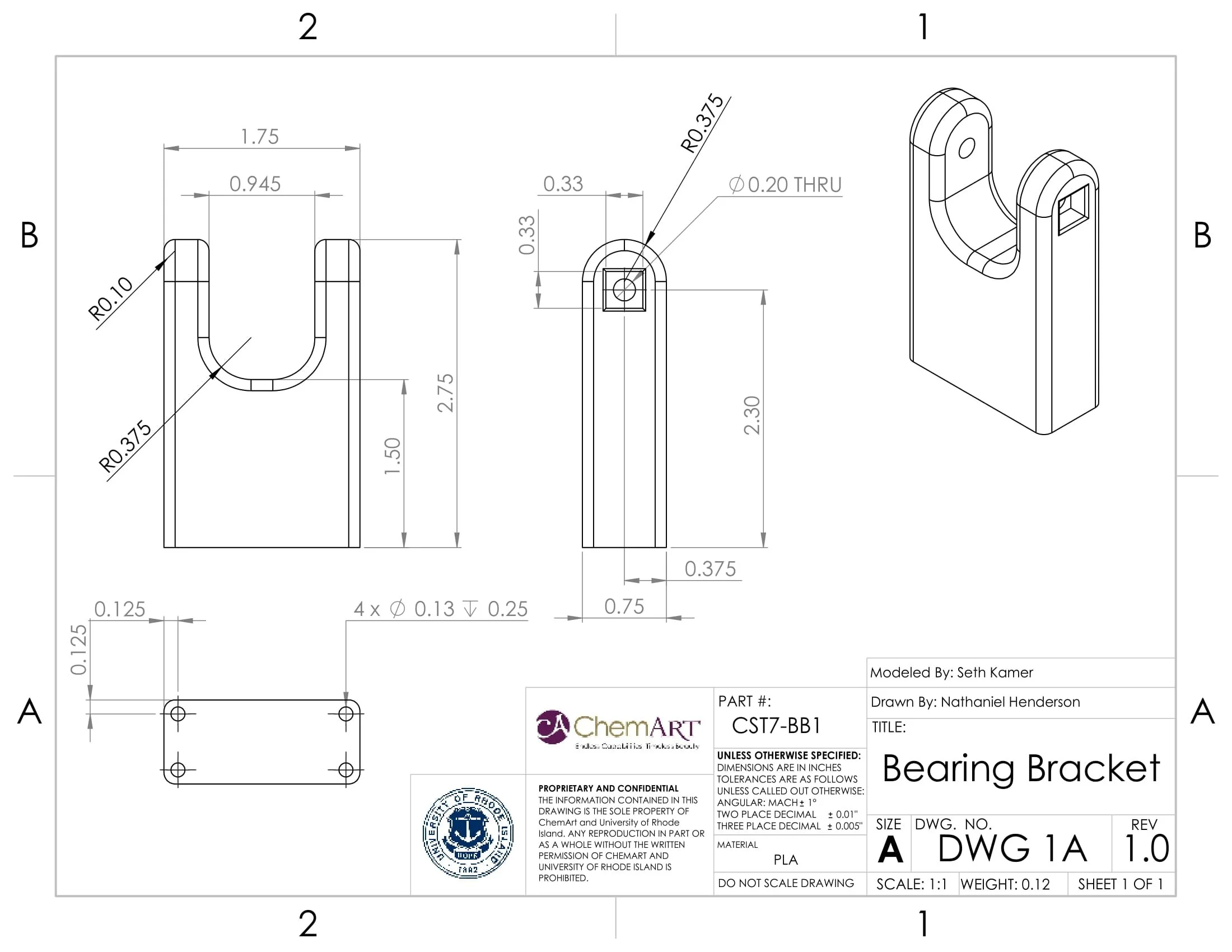
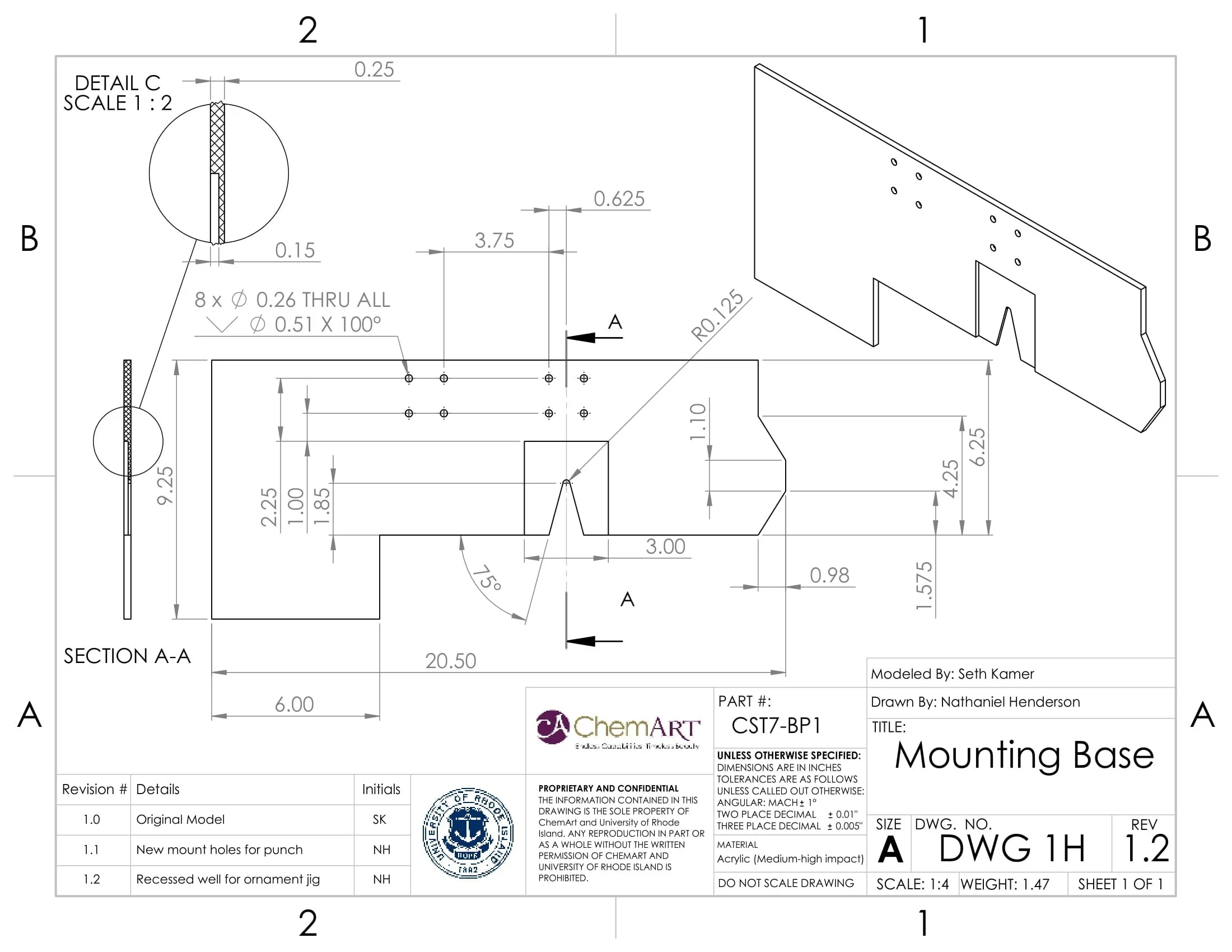


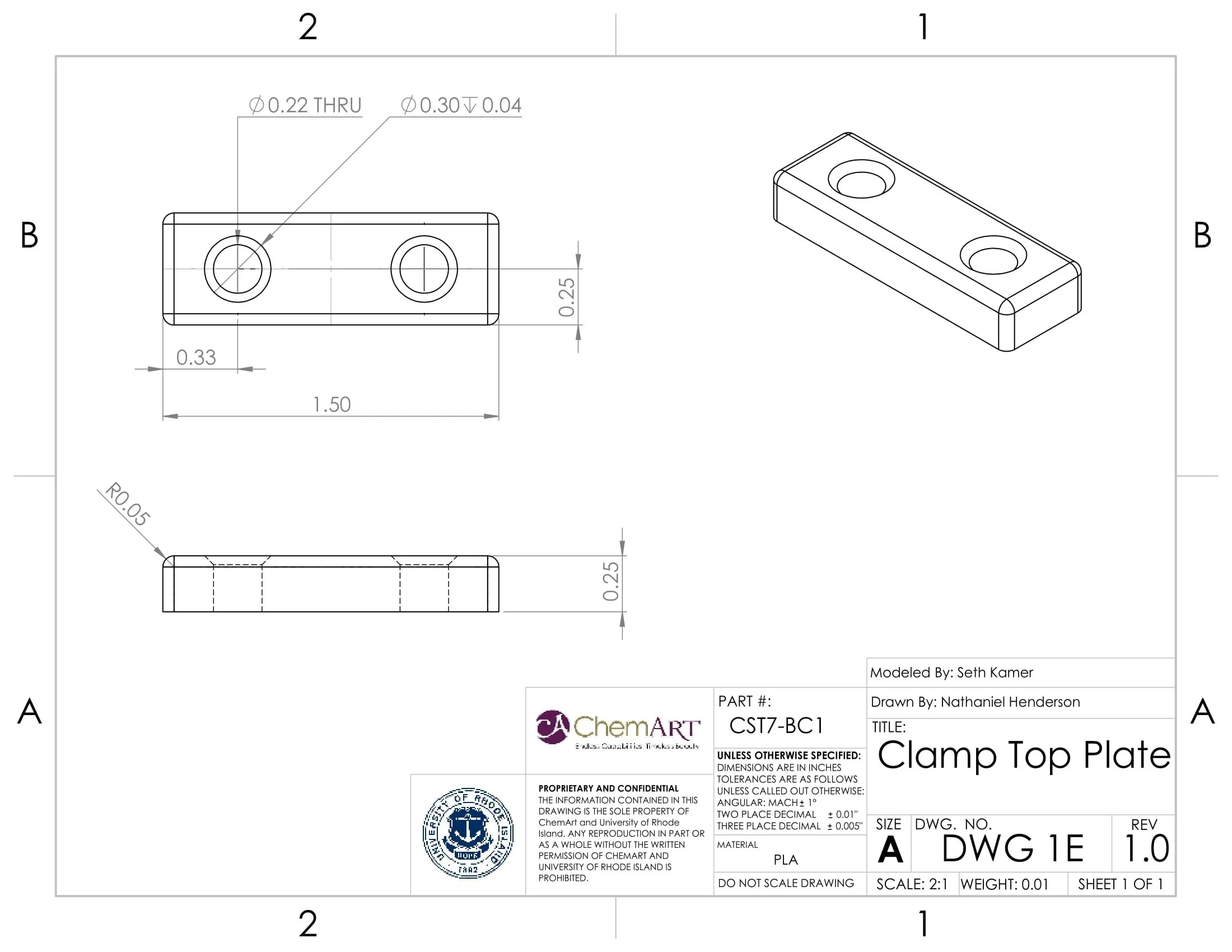


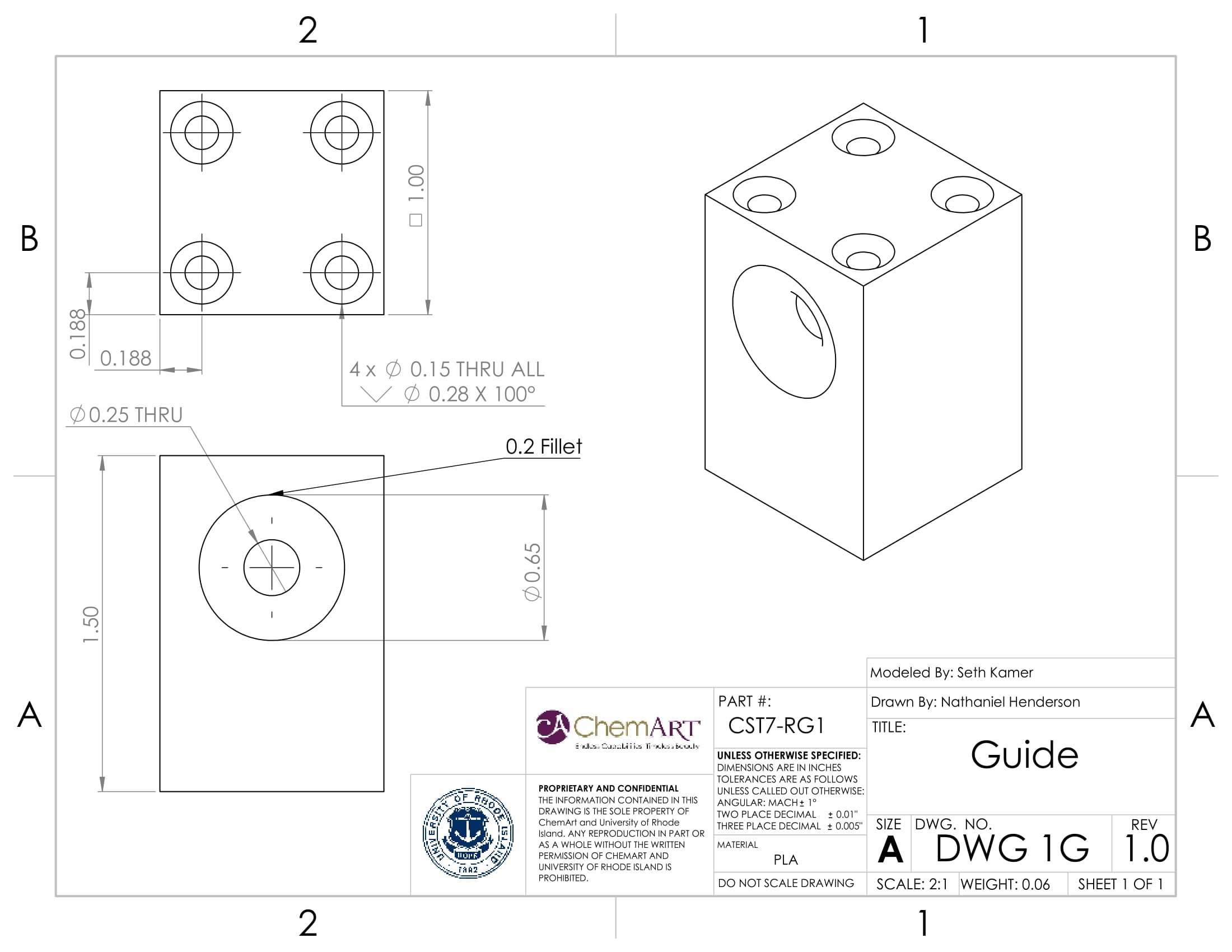
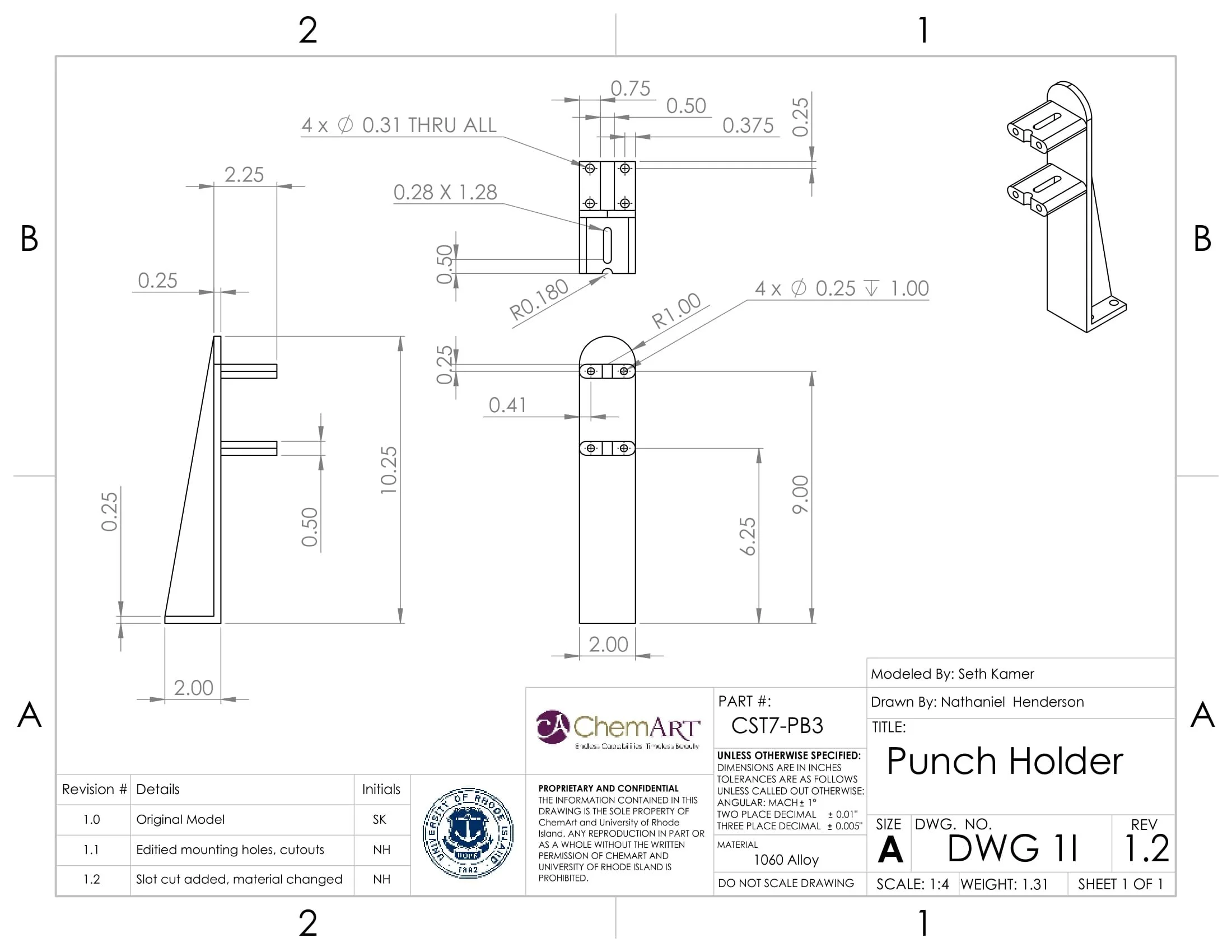
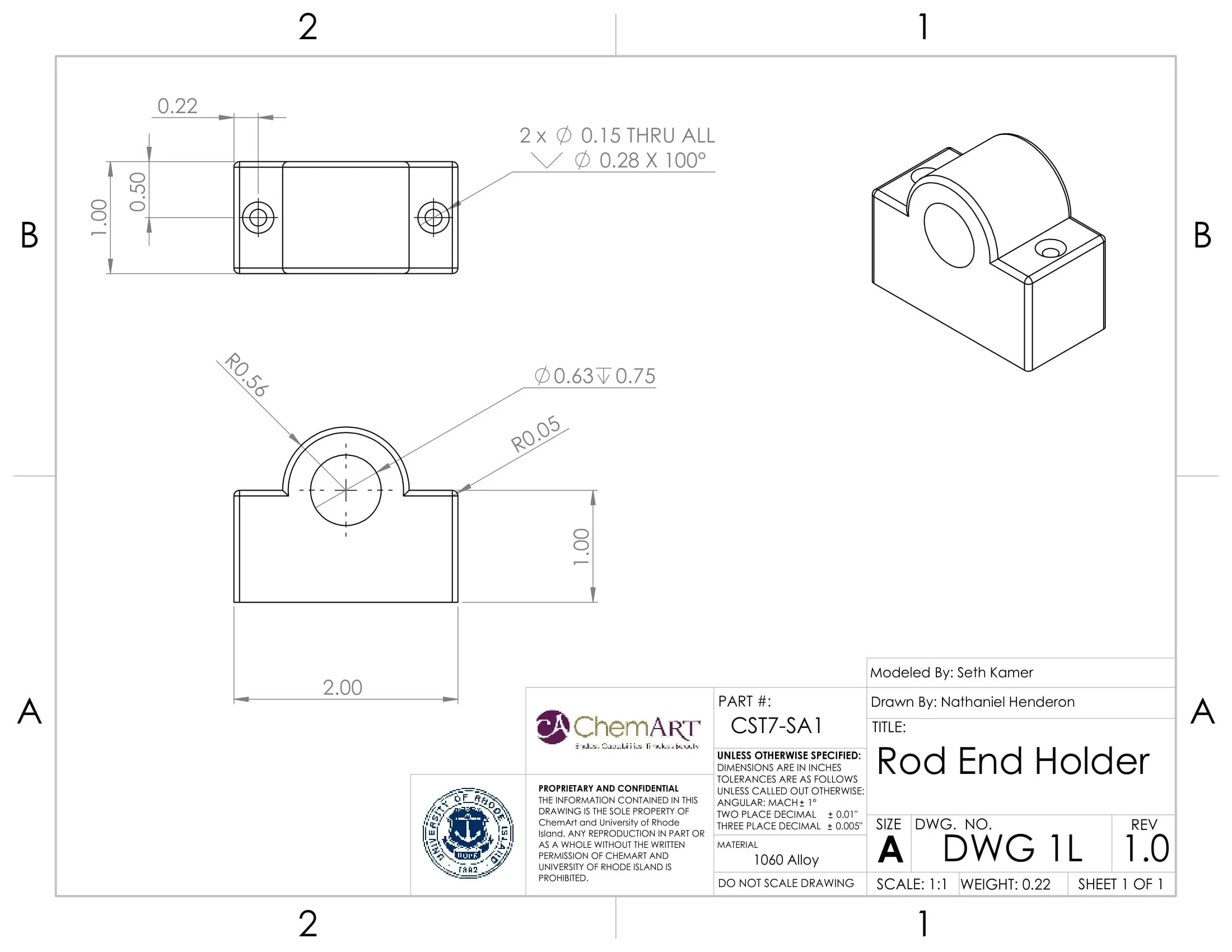
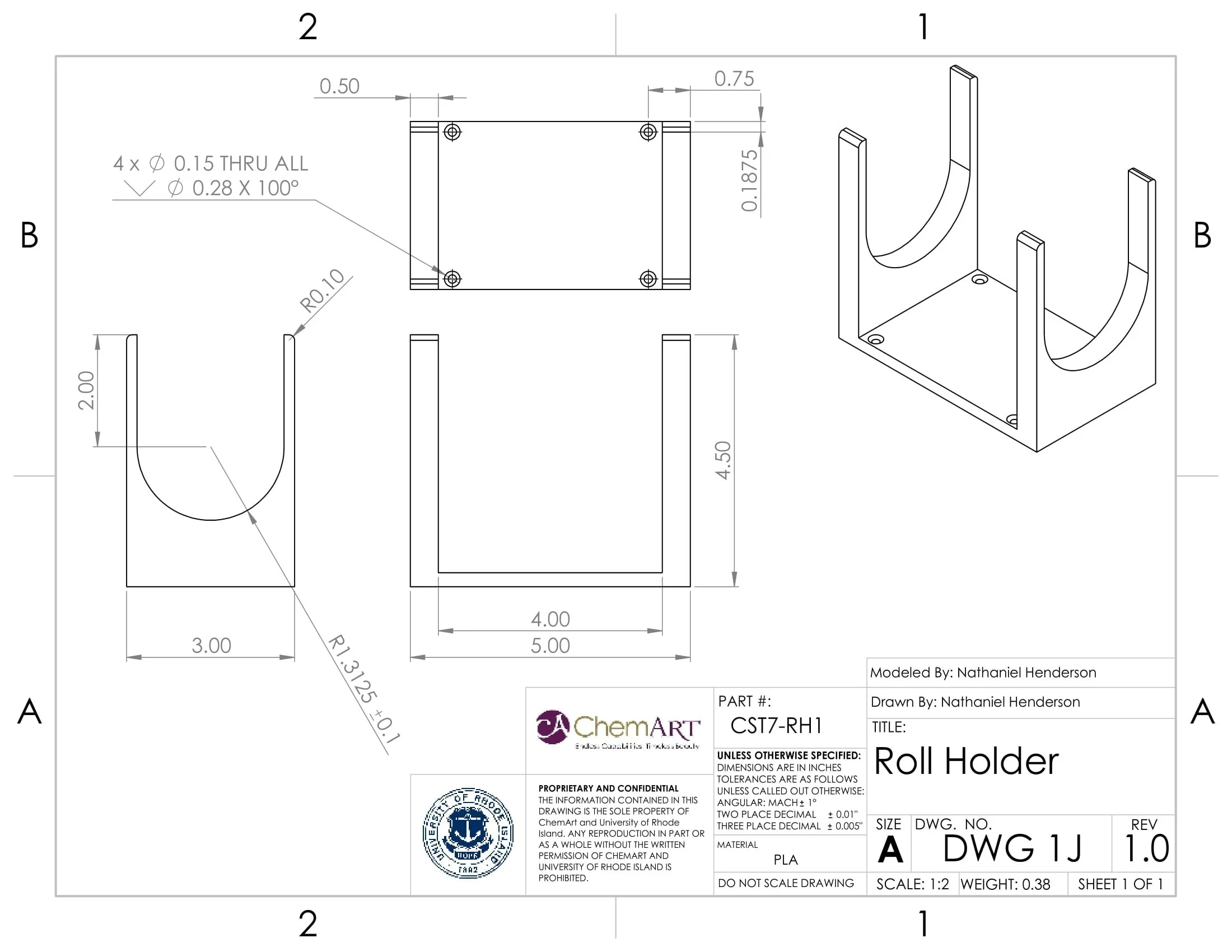
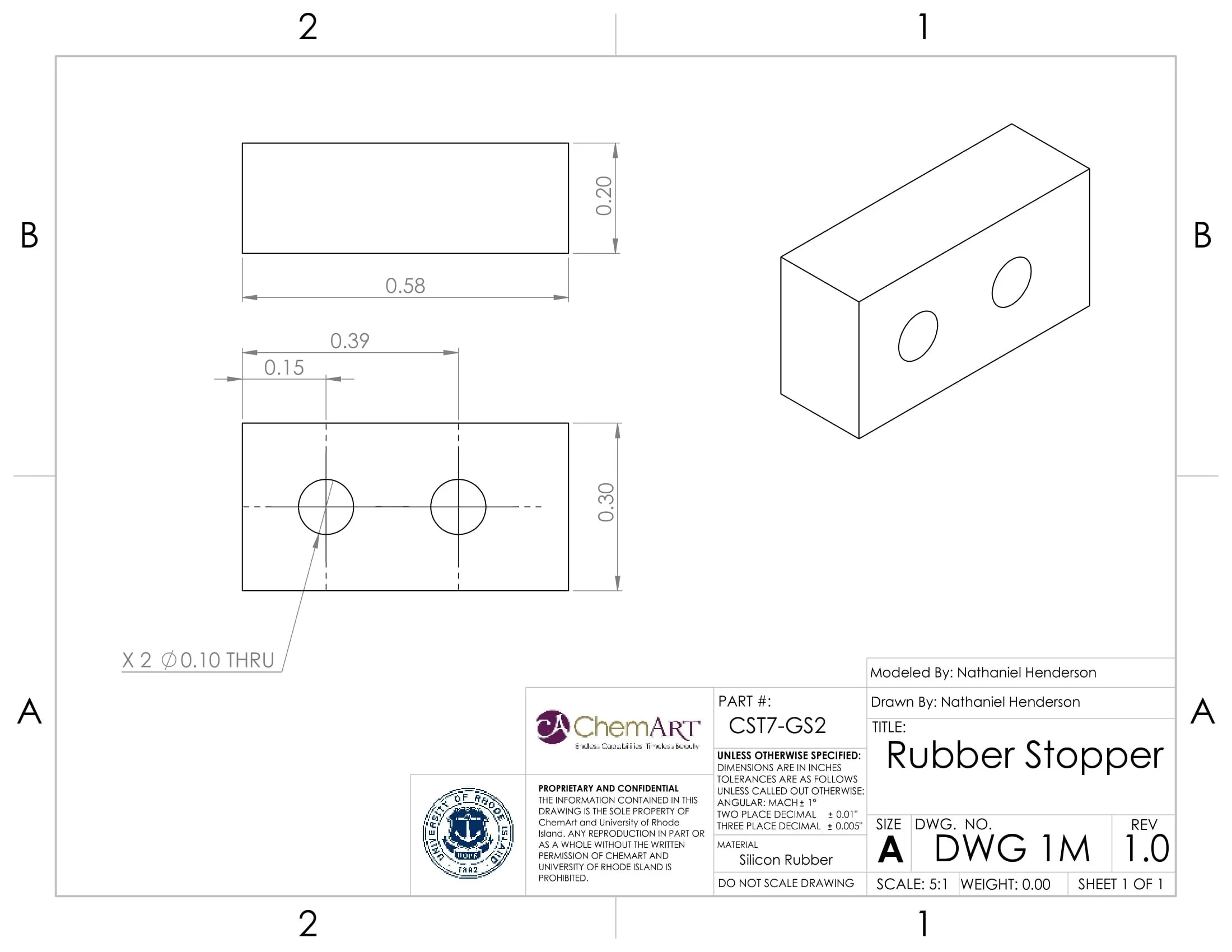
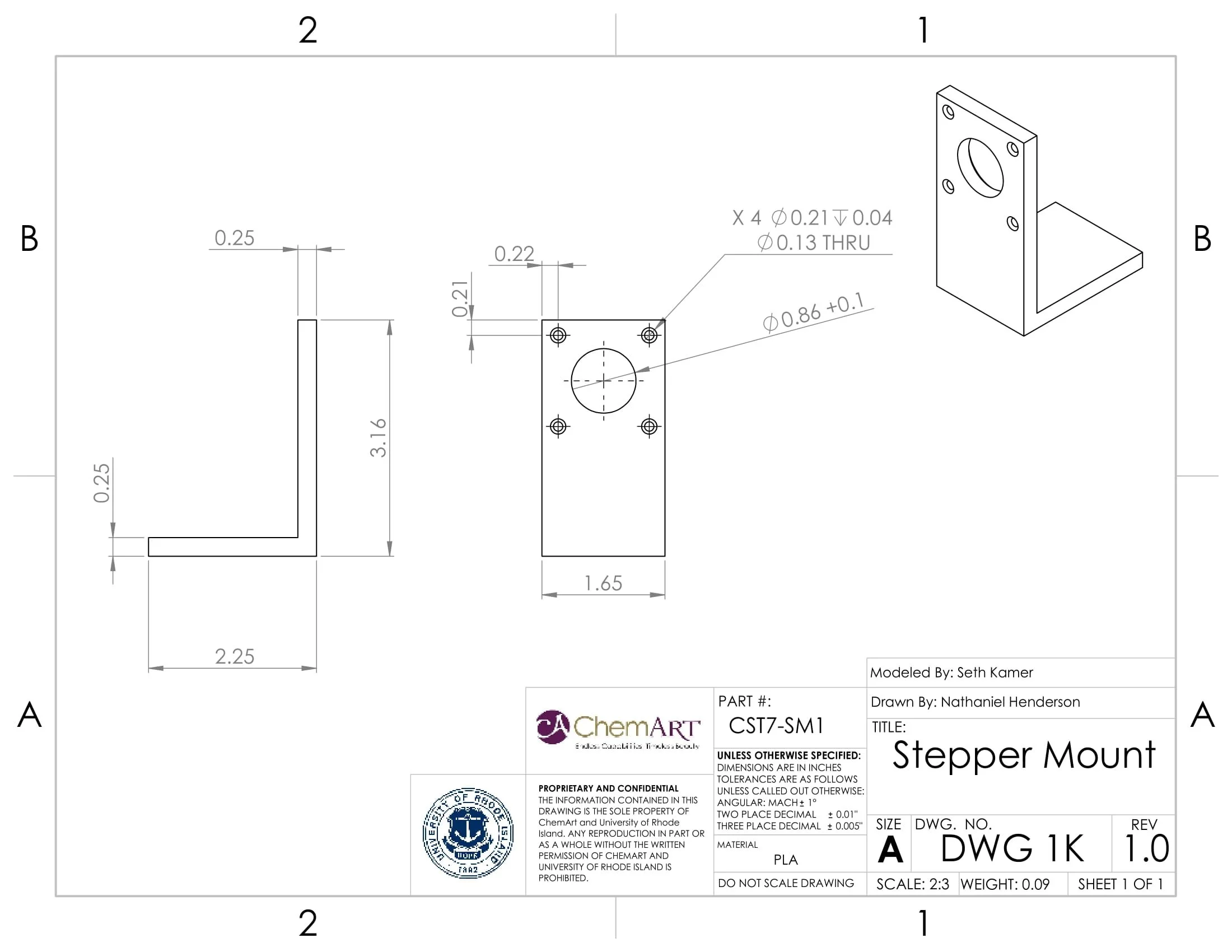